Généralités :
Les techniques et les essais pour tester les matériaux sont devenus plus précis au fil du temps, le progrès technologique des capteurs et des conditionneurs électroniques ont permis de s’affranchir de nombreuses erreurs provenant des machines d’essais afin de mieux déterminer les propriétés mécaniques des métaux.
Un des sujets les plus intéressant est de déterminer la limite de fatigue des matériaux et d’estimer leur durabilité dans différents milieux et sous diverses sollicitations plus ou moins combinées.
La plus grande polyvalence vient des systèmes d’essai servo-hydrauliques en boucle fermée qui offrent la capacité de contrôler n’importe laquelle des variables prépondérantes de fatigue, à condition que cette variable puisse être détectée électroniquement.
Les machines servo-hydrauliques à contrainte directe peuvent être exploitées en charge constante, en déformation ou en contrôle de déplacement en fonction du signal variable qui est détecté et renvoyé dans la boucle servocommandée.
Toutes les machines d’essais de fatigue ont un châssis de chargement de base qui résiste aux charges imposées sur l’éprouvette. Ce cadre prend également en charge un certain nombre d’autres composants, y compris le mécanisme d’entraînement qui transmet la charge à l’échantillon via des mors, des cellules de charge, un système d’extensométrie et d’autres appareils de mesure.
Les attributs clés du cadre de chargement sont de fournir un espace accessible pour l’installation et le retrait des éprouvettes.
Une fois installé, il présente une rigidité très élevée par rapport à la rigidité de l’échantillon.
En d’autres termes, la machine d’essai doit subir le moins de déplacement de charge élastique possible. Idéalement, l’essentiel du déplacement doit être absorbé par l’échantillon.
Le train de chargement à l’intérieur de la machine d’essai doit également avoir un excellent alignement de la ligne de charge avec l’échantillon pour éviter une déformation ou un flambage prématuré de l’échantillon sous des charges élevées. La classe 5 suivant la norme ASTM E 1012 est très souvent requise.
Applications pratiques des essais dynamiques :
La machine d’essai de fatigue sous contrainte directe soumet une éprouvette à une contrainte ou une déformation uniforme à travers sa section transversale.
Pour une même section transversale, une machine d’essais de fatigue axiale doit pouvoir appliquer une force plus importante qu’une machine statique pour obtenir la même contrainte.
Les machines axiales sont utilisées pour obtenir des données de fatigue pour la plupart des applications et offrent la meilleure méthode pour établir, par contrôle en boucle fermée, une plage de déformation contrôlée dans le régime de déformation plastique (fatigue à faible cycle).
Les systèmes servo-hydrauliques en boucle fermée offrent un contrôle, une surveillance et une polyvalence optimale.
Afin d’obtenir des essais reproductibles, ces essais de fatigue sont réalisés à partir d’éprouvettes normalisées ayant des caractéristiques métrologiques précises.
La machine de fatigue doit également être vérifiée en dynamique suivant la norme NF EN ISO 4965-1 et ou la norme ASTM E467. CVM réalise la vérification dynamique sous accréditation Cofrac des machines de fatigue.
L’approche contrainte-durée semble la mieux applicable aux composants qui ressemblent aux échantillons d’essai et qui sont approximativement de la même taille (cela satisfait la similitude associée à l’utilisation de la séparation totale comme critère de rupture).
Une grande partie de la technologie en application de cette approche est basée sur les métaux ferreux, en particulier les aciers.
Les aciers sont prédominants en tant que matériau de structure, mais les aciers affichent également une limite de fatigue ou une limite d’endurance à un nombre élevé de cycles (généralement> 107 cycles) dans des conditions environnementales normales.
Il est préférable d’appliquer les sollicitations dans le domaine élastique ou à proximité, pour traiter des situations de charge d’amplitude constante dans ce qu’on va appeler le régime de durée de « vie infinie ».
Courbes de WÖHLER
La représentation graphique la plus connue est la courbe de WÖHLER appelée également courbe S-N (Stresses – Number of cycles).
Les pièces sont soumises à des cycles d’effort répétés et on note le nombre de cycles au bout duquel, la rupture se produit.
Ce nombre de cycle est reporté en abscisse sur une échelle logarithmique et la contrainte est reportée en ordonnée.
Exemple de courbe de WÖHLER
L’asymptote horizontale correspond à une contrainte qui représente la limite de Fatigue.
On remarque la présence de 3 domaines :
- Domaine Oligocyclique : ruptures rapides sous fortes contraintes.
- Domaine d’endurance limitée : ruptures systématiques sous un nombre limité de cycles.
- Domaine d’endurance illimitée : aucune rupture sous une contrainte donnée.
Attention : d’autres alliages que l’acier dans des environnements plus agressifs ne présentent pas forcément de limite de fatigue.
Un nombre significatif d’essai est nécessaire pour obtenir ce type de courbe qui sera impactée par la qualité de la machine d’essai et la dispersion liée aux éprouvettes (usinage, matériaux,…). Une machine de fatigue étalonner en dynamique permet de garantir des résultats fiables.
Essais CTOD (Crack Tip Opening Displacement)
L’essai CTOD est un essai basé sur la mécanique de la rupture qui est utilisé quand quelque déformation plastique précède une rupture catastrophique.
L’éprouvette CTOD est pourvue d’une fissure réelle obtenue par un essai de fatigue et est mise sous charge de telle façon que la vitesse de l’essai correspond mieux aux conditions de service.
Pré-fissuration en flexion 3 points d’une éprouvette SEB : CTOD
L’éprouvette est proportionnelle, c.-à-d. que la longueur, la profondeur et la largeur de chaque éprouvette sont liées entre elles de sorte que, indépendamment de l’épaisseur du matériau, chaque éprouvette a des dimensions uniformes.
Comme la longueur de la fissure et l’ouverture sont connues, il suffit d’une simple somme géométrique pour calculer l’ouverture en fond de fissure.
Durant l’essai, la charge et l’ouverture sont automatiquement enregistrées sur un graphique.
Un tel graphique est comparable à une courbe de traction.
Essais K1c et J1c
Le principal objectif du test de ténacité à la rupture est de produire un résultat qui peut être utilisé pour évaluer quantitativement la résistance d’un matériau ou d’une structure à l’extension d’un défaut semblable à une fissure.
Cela implique le test d’un échantillon contenant une fissure sous une force ou un déplacement augmentant de façon monotone.
L’essai se poursuit jusqu’à ce que l’échantillon atteigne ou dépasse un point ou une région sur lequel la ténacité à la rupture est définie.
Cela peut être un point qui marque la séparation complète de l’échantillon (rupture) ou un point qui marque le début du processus d’extension stable des fissures qui résulte du comportement de rupture ductile.
La ténacité à la rupture pouvant dépendre de la taille et de la géométrie de l’échantillon, l’essai doit être effectué avec un échantillon de taille suffisante et d’une géométrie donnée pour satisfaire aux conditions données dans la norme.
L’équipement utilisé doit comprendre une machine d’essai ayant la capacité requise pour appliquer la force, un ensemble de dispositifs de chargement, une instrumentation avec la précision correcte et un étalonnage pour générer les données utilisées dans l’évaluation de la ténacité à la rupture.
Exemple d’éprouvette CT pour essai K1c avec fixation externe du capteur d’ouverture
Pour les aciers de construction en présence de plasticité à grande échelle, la mécanique de rupture élastique linéaire ne peut pas caractériser avec précision le comportement de rupture, et donc un autre modèle de mécanique de rupture non linéaire est nécessaire. Sur la base de la théorie de la déformation de la plasticité, un nouveau paramètre de fracture a été appelé intégrale J et est défini comme :
Si le test de ténacité à la rupture vise à déterminer l’intégrale J, alors l’énergie de déformation de l’éprouvette doit être mesurée, ce qui nécessite la mesure du déplacement des points de chargement, du déplacement du point de charge, LPD (ou déplacement de la ligne de charge).
Essais de fissuration (courbes Da/dN)
Typiquement ces essais se font sur une tôle avec une fissure centrale chargée en traction oscillante. On mesure l’évolution de la longueur de la fente (2a) en fonction du nombre de cycles. Cette longueur se mesure soit optiquement soit en fonction de paramètres électriques.
Pour chaque niveau de chargement on peut ainsi en déduire une vitesse de propagation da/dN en fonction de la longueur de la fissure.
Sous cette forme, les résultats d’essais de fissurations ne sont pas facilement exploitables, puisque qu’ils sont fonction de la taille de la fente et des conditions d’essai (amplitude de contrainte, géométrie,…).
On utilise la loi de PARIS pour introduire l’amplitude du facteur de concentration des contraintes : DK
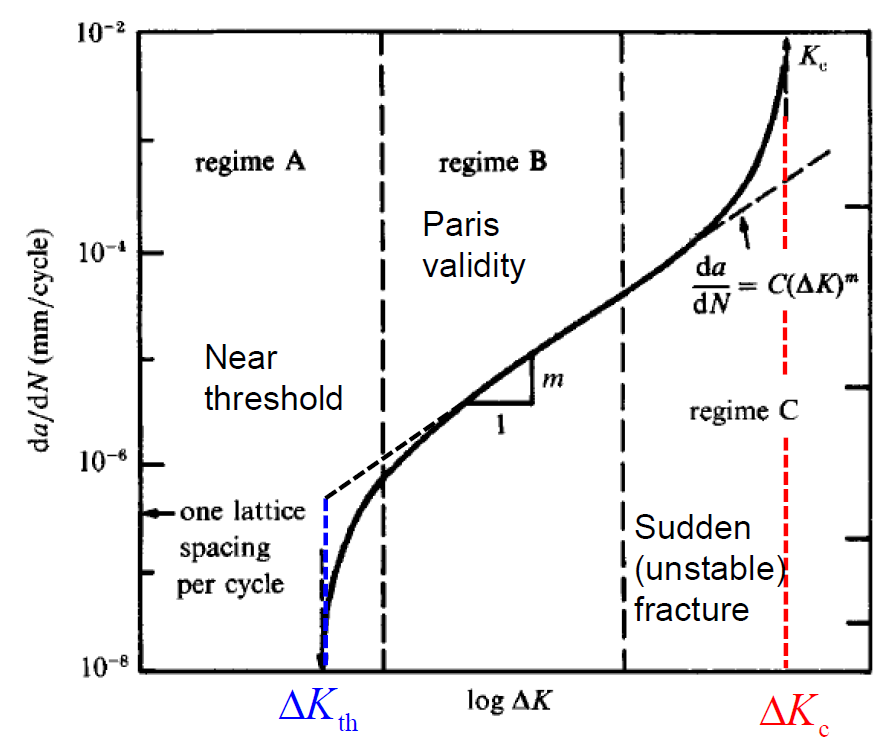
DKth est la plage du facteur d’intensité de contrainte, en dessous de cette amplitude, la fissure reste de la même taille malgré la fatigue
DKC est la plage du facteur d’intensité de contrainte pour laquelle Kmax = KIc, En approchant de cette valeur, la fissure se transforme en propagation instable
Référentiels normatifs :
Essais de fatigue à grand nombre de cycles HCF | |
ISO 1099 | Metallic materials – Fatigue testing – Axial force-controlled method. |
ASTM E466 | Standard Practice for Conducting Force Controlled Constant Amplitude Axial Fatigue Tests of Metallic Materials |
NF EN 6072 | Essai de fatigue à amplitude constante |
NF EN 3987 | Essais de fatigue mégacyclique en contraintes imposées |
Essais de fatigue oligocyclique LCF | |
ISO 12106 | Matériaux métalliques – Essais de fatigue – Méthode par détermination axiale contrôlée |
ASTM E606 | Standard practice for strain controlled fatigue testing |
Détermination du facteur critique d’intensité de contrainte K1C | |
ISO 12737 | Détermination du facteur critique d’intensité de contrainte |
ASTM E399 | Standard test method for plain-strain fracture toughness of metallic materials |
ASTM E1820 | Standard Test Method for Measurement of Fracture Toughness |
ISO 15653 | Méthode d’essai pour la détermination de la ténacité quasi statique à la rupture des soudures |
ISO 12135 | Méthode unifiée d’essai pour la détermination de la ténacité quasi statique |
Réalisation d’essais de vitesse de propagation | |
ISO 12108 | Méthode d’essai de propagation de fissure en fatigue |
ASTM E647 | Standard test method for measurement of fatigue crack growth rates |
Essais d’endurance (Médical) | |
ISO 7206-4 | Détermination des propriétés d’endurance et des performances des tiges fémorales |
ISO 7206-6 | Exigences de performance et essais des propriétés d’endurance de la région du col des tiges fémorales |
ISO 14879-1 | Détermination des propriétés d’endurance des embases tibiales |
Autres | |
LAB GTA 16 | Guide technique d’accréditation en essais des matériaux métalliques |
NADCAP 7101/3 | Mechanical Testing |
Erreurs et incertitudes
Malgré les nombreuses précautions prises, de nombreuses variables influencent les résultats des essais de fatigue.
Tous les systèmes de mesure de force nécessitent un étalonnage périodique pour garantir leur précision. Les méthodes de vérification et les intervalles auxquels elles sont effectuées sont spécifiés dans des normes telles que l’ASTM E4 ou l’ISO 7500-1.
Il faut veiller à ce que le serrage des mors n’entraîne pas un désalignement et, par conséquent, des contraintes indésirables dans la section d’essai de l’échantillon.
Pour obtenir des données de fatigue précises, il est essentiel de s’assurer que la charge appliquée est alignée avec l’axe de l’échantillon.
Ceci est particulièrement important pour les échantillons chargés axialement.
Un alignement médiocre et non reproductible produit des déformations de flexion qui réduisent la durée de vie en fatigue et augmentent la dispersion dans les données.
En fait, il a été déterminé que le plus grand facteur contribuant à la dispersion dans les données LCF (Low Cycle Fatigue) est dû à de la flexion.
Des contraintes de flexion surviennent en cas de désalignement quelque part dans le train de charge. L’axialité et la concentricité de l’actionneur, des mors, de l’éprouvette et du capteur de force doivent être vérifiées et corrigées en cas de problème.
Des ajustements grossiers peuvent être effectués en supprimant la précharge et en desserrant le train de charges.
Ces composants peuvent ensuite être déplacés et / ou calés pour obtenir un alignement correct.
Une fois le train de charges resserré, les petites déformations de flexion, qui existent toujours, doivent être mesurées et minimisées.
Cela se fait généralement en utilisant un échantillon d’essai à jauge de contrainte, qui permet de calculer les déformations de flexion en fonction de la position le long de l’échantillon d’essai, en utilisant le même matériau et la même configuration d’essai que ceux utilisés dans le programme d’essai réel.
Pendant le chargement axial, les déformations de flexion doivent être maintenues en dessous d’une quantité spécifiée, comme décrit dans diverses normes d’essai de fatigue.
Par exemple, l’ASTM E606 recommande que la déformation de flexion maximale ne dépasse pas 5% de la plage de déformation axiale minimale utilisée pendant l’essai.
Si les déformations de flexion dépassent ces quantités, le banc d’essai doit être réaligné.
Le dispositif de CVM qui s’adapte à une extrémité du train de charges, permet le réglage des composants angulaires et concentriques de flexion alors que le train de charge est en précharge.
De plus, le logiciel associé permet en temps réel de connaitre les erreurs d’alignement et donc de les corriger.
Il y a tout simplement aucun moyen d’effectuer un test sur matériaux qui contienne zéro erreur ou une valeur nulle pour l’incertitude de mesure.
En cours de test, un matériau ou un composant peut conduire à des problèmes de sécurité, de garantie et de responsabilité à la suite de défaillance ou dommage prématuré.
C’est particulièrement une préoccupation pour le transport et l’industrie médicale.
Dans des conditions de test existant, la non-conformité peut être prononcé lorsque les forces ne sont pas atteintes et ou que la vitesse, la fréquence ou le nombre de cycles est inférieur au requis pour répondre aux critères de conformité.
Effectuer un étalonnage dynamique de la machine d’essai est la seule méthode efficace pour quantifier la mesure des erreurs affectant la performance du système dynamique.
L’accréditation de CVM vous apporte un gage de garantie sur les résultats et les incertitudes associées.
CVM dispose de l’ensemble des essais accrédités pour vérifier vos machines d’essais :
- Force (statique : ASTM E4 et ISO 7500-1 et dynamique : ISO 4695-1 Méthode A et ASTM E467)
- Extensométrie (ISO 9513 et ASTM E83)
- Alignement (ASTM E1012)
Les procédures d’étalonnage / vérification en dynamique sont spécifiées dans ;
– ISO 4965-1 : Matériaux métalliques — Étalonnage de la force dynamique uniaxiale pour les essais de fatigue — Partie 1 : Systèmes d’essai
– ISO 4965-2 : Matériaux métalliques — Étalonnage de la force dynamique uniaxiale pour les essais de fatigue — Partie 2 : Instrumentation pour équipement d’étalonnage dynamique
– ASTM E467 : Standard Practice for Verification of Constant Amplitude Dynamic Forces in an Axial Fatigue Testing System
On peut lister les erreurs contributives des sources associées aux forces dynamiques des machines d’essai de fatigue à amplitude constante.
Il est relativement facile de déterminer la mesure incertitude liée au fonctionnement statique d’une machine d’essai de fatigue.
Déterminer la mesure de l’incertitude et ou l’évaluation des performances d’essai de la machine dans des conditions dynamiques est plus complexe.
Des erreurs d’accélération se produisent en raison de la dérive de la force du système indiqué par la machine et la quantité de masse entre la partie mobile de l’indication de force de la machine et l’échantillon.
Ces erreurs peuvent être insignifiantes selon la fréquence, les niveaux d’effort cycliques et les configurations des machines.
D’autre part, les erreurs d’accélération induites dynamiquement peuvent être assez grandes.
Pour certains essais nécessitant une haute fréquence et des forces relativement importantes, les erreurs peuvent être anticipées (technique de compensation de masse avec un accéléromètre monté sur la masse en mouvement).
Si une compensation de masse est appliquée pendant les essais, la vérification doit être effectuée avec la compensation appliquée.
Liste des éléments de la machine qui affectent les performances dynamiques des essais de fatigue :
- Rigidité du cadre
- Rigidité de l’échantillon
- Masse en mouvement
- Déflexion de la masse en mouvement
- Résonance de la machine
- Frottement de l’actionneur
Paramètres de essais qui affectent les performances dynamiques des machines d’essais de fatigue:
- Niveaux de force cyclique
- La fréquence
- Forme du signal de fréquence (Sinusoïdale, carré, …)
Sources d’incertitudes
Étalonnage statique de la machine d’essai
Étalonnage statique du dynamomètre et de l’instrumentation
Instrumentation d’acquisition de données (machine)
Instrumentation d’acquisition de données (dynamomètre)
Normes | Paramètres | Incertitude type | a | DK | |||
ASTM E647 | Alignement | B | 2 | 1 | 0 | ||
Force | B | 0 | 1 | 0 | |||
Dérive de la force | B | 0 | 2 | 0 | |||
Variation du signal, bruit, amplification | A | 2 | 1 | 1 | |||
Normes | Paramètres | Incertitude type | d | F | Vp | ||
ASTM E1290
(CTOD) |
Alignement | B | 2 | 2 | 2 | ||
Normes | Paramètres | Incertitude type | Nf | E0, E1, E2 | smax/min | Dep | |
ASTM E606 | Alignement | B | 1 | 5 | 2 | 2 | |
Force | B | 0 | 1 | 1 | 2 | ||
Dérive | B | 2 | 0 | 1 | 2 | ||
Contrôle des limites | B | 2 | 0 | 2 | 2 | ||
Normes | Paramètres | Incertitude type | sD | Kt | Kf | ||
ASTM E466 | Etalonnage cellule | B | 1 | 1 | 1 | ||
Alignement | B | 1 | 1 | 1 | |||
Contrôle dynamique de la force | B | 1 | 1 | 1 | |||
Dérive de la force | B | 1 | 1 | 1 | |||
Fréquence d’essai | 0 | ||||||
Normes | Paramètres | Incertitude type | K1c | PQ | |||
ASTM E399 | Alignement | B | 2 | 2 | |||
Force | B | 2 | 2 |
Paramètre ayant une contribution dans l’incertitude des résultats.
1 : Impact significatif
2 : Impact modéré
0 : Pas d’impact
L’objectif des vérifications sous accréditation Cofrac proposées par CVM est de vous apporter l’assurance que vos équipements soient conformes aux normes en vigueur, d’assurer leur traçabilité métrologique et la validité de vos résultats lors des essais de fatigue.
Les rapports remis par CVM vous permettent également de connaitre les contributions majeures sur vos incertitudes afin de réaliser les plans d’action utiles et nécessaires pour les réduire.
Certaines machines peuvent rentrer en résonnance à certaines fréquences, l’étalonnage dynamique vous assure que les fréquences que vous utilisez sont cohérentes avec l’ensemble de vos essais.
CVM est le seul interlocuteur pour une prestation complète sur l’ensemble de vos vérifications.
Quelques définitions
Termes | Reference | Définitions |
Amplitude | ASTM E467 | La moitié de la mesure crête à crête de la forme d’onde cyclique |
Force indiquée | ASTM E467 | La valeur de force fournie par le capteur de force ou la lecture du dynamomètre (par exemple, une sortie numérique ou graphique pour la lecture, y compris une capacité de prélèvement en crête) ; ces valeurs sont généralement obtenues à partir d’un voltmètre numérique (DVM) ou de fichiers générés par une acquisition de données informatisée |
Force indiquée Fi | ISO 4965-01 | Force mesurée et indiquée par le capteur de force étalonné du système d’essai dynamique dans des conditions statiques et dynamiques |
Forces dynamiques indiquées | ASTM E467 | Les forces maximales et minimales rapportées par la machine d’essai pendant une partie d’un essai dynamique. Ces valeurs sont généralement obtenues à l’aide d’un oscilloscope, d’un compteur de crête-vallée ou de fichiers générés par acquisition de données informatisée. |
Ecart | — | Erreur de précision relative de la force dynamique indiquée de la machine d’essai |
Erreur indiquée ei | ISO 4965-01 | Différence dans les plages de force indiquées par le système d’essai et le dispositif d’étalonnage dynamique (DCD), exprimée en pourcentage de la plage de force DCD |
Capteur | ASTM E467 | Un appareil de mesure qui a un signal de sortie proportionnel à la quantité mesurée, la tension électrique augmente généralement linéairement avec la force appliquée. Le système de test peut utiliser cette tension pour le contrôle. |
Facteur de conversion | ASTM E467 | Le facteur de conversion entre la force du dynamomètre et la force indiquée |
Facteur de correction C | ISO 4965-01 | Rapport entre la plage de force dynamique déterminée par un DCD (ΔFDCD) et la plage de force dynamique indiquée par le système de test (ΔFi), à la même fréquence de test |
Fonction de conversion | BS 7935-1 | Rapport entre la plage de force dynamique déterminée par une réplique et la plage de force dynamique indiquée par un système d’essai donné, à une fréquence donnée |
Matériel d’acquisition de données | ASTM E467 | L’équipement utilisé pour convertir une force conditionnée en une force indiquée |
Termes | Reference | Définitions |
Erreurs dynamiques | ASTM E467 | Erreurs dans la sortie de force corrigée du capteur de force qui se produisent en raison du fonctionnement dynamique (avec des erreurs de flexion de l’échantillon intentionnellement corrigées) |
Niveau final | ASTM E467 | Soit un niveau maximum ou minimum pour une forme d’onde cyclique |
Force du dynamomètre | ASTM E467 | La valeur de force fournie par la lecture du dynamomètre |
Force conditionnée | ASTM E467 | La tension de haut niveau ou les données numériques disponibles à partir du dynamomètre ou de l’instrumentation de conditionnement du signal du capteur de force ; elle est souvent utile lors de la vérification dynamique car elle peut être surveillée plus facilement par une instrumentation de mesure autonome |
Force corrigé | ASTM E467 | La force obtenue après application d’un facteur de correction dynamique à la force indiquée par le capteur de force |
Commande de force | ASTM E467 | La force souhaitée à appliquer à l’échantillon ou au dynamomètre par la machine d’essai |
Vallée | ASTM E467 | Le niveau minimum d’un cycle |
Dynamomètre | ASTM E467 | Un dispositif d’étalonnage élastique utilisé pour indiquer les forces appliquées par un système d’essai de fatigue pendant le fonctionnement dynamique. Un échantillon à jauge de contrainte est souvent utilisé comme dynamomètre. Une instrumentation de capteur approprié est également requise pour fournir des lectures précises sur la plage de fréquence et de force prévue. |
Dispositif d’étalonnage dynamique DCD | ISO 4965-01 | Pour la méthode A, une réplique à jauge de contrainte ayant la même masse et la même rigidité que les échantillons à tester. Pour la méthode B, une éprouvette réplique à jauge de contrainte ou un dispositif d’essai, de rigidité connue |
Termes | Reference | Définitions |
Système de calibration | BS 7935-1+2 | Eprouvette réplique ou dispositif d’essai |
Pic | ASTM E467 | Le niveau maximum sur un cycle |
Amplitude | ASTM E467 | La valeur absolue du pic moins la vallée pour une forme d’onde cyclique |
Plage de forces dynamiques ΔF | ISO 4965-1 | Différence entre les valeurs de force maximale (crête) et minimale (vallée) dans des conditions cycliques |
Plage de forces | BS 7935-1 | Différence entre les valeurs maximales et minimales de force dans des conditions cycliques |
Machine d’essai de fatigue | ASTM E467 | Dispositif pour appliquer des cycles de force répétés à un échantillon ou à un composant, qui applique des cycles de force répétés de même envergure, fréquence, forme d’onde, niveau moyen et niveaux finaux |
Peak picking | ASTM E467 | Processus de détermination du pic ou de la vallée d’une forme d’onde cyclique |
Force vraie | ASTM E467 | La force réelle appliquée à l’échantillon ou au dynamomètre |
Répétabilité | ASTM E467 | L’étroitesse d’accord entre des mesures répétées des forces dynamiques dans les mêmes conditions |